5 Ways to Reduce Time Delays in a Demolition
Let's face it: Abatement and demolition projects are not the sorts of projects you want over-budget or behind schedule. This is why experience makes a world of difference. It's one thing to plan the steps in a demolition or abatement project—but another thing entirely to know what causes demolition delays, and how to prevent them.
For example, here are five things we offer with our full-service demolition offerings precisely to prevent demolition delays and problems:
We Use Our Own Equipment
When you use your own equipment for a demolition project, you are in control of their servicing and maintenance. Staying on top of the condition of equipment helps reduce issues with it breaking down, or simply being unavailable for a job.
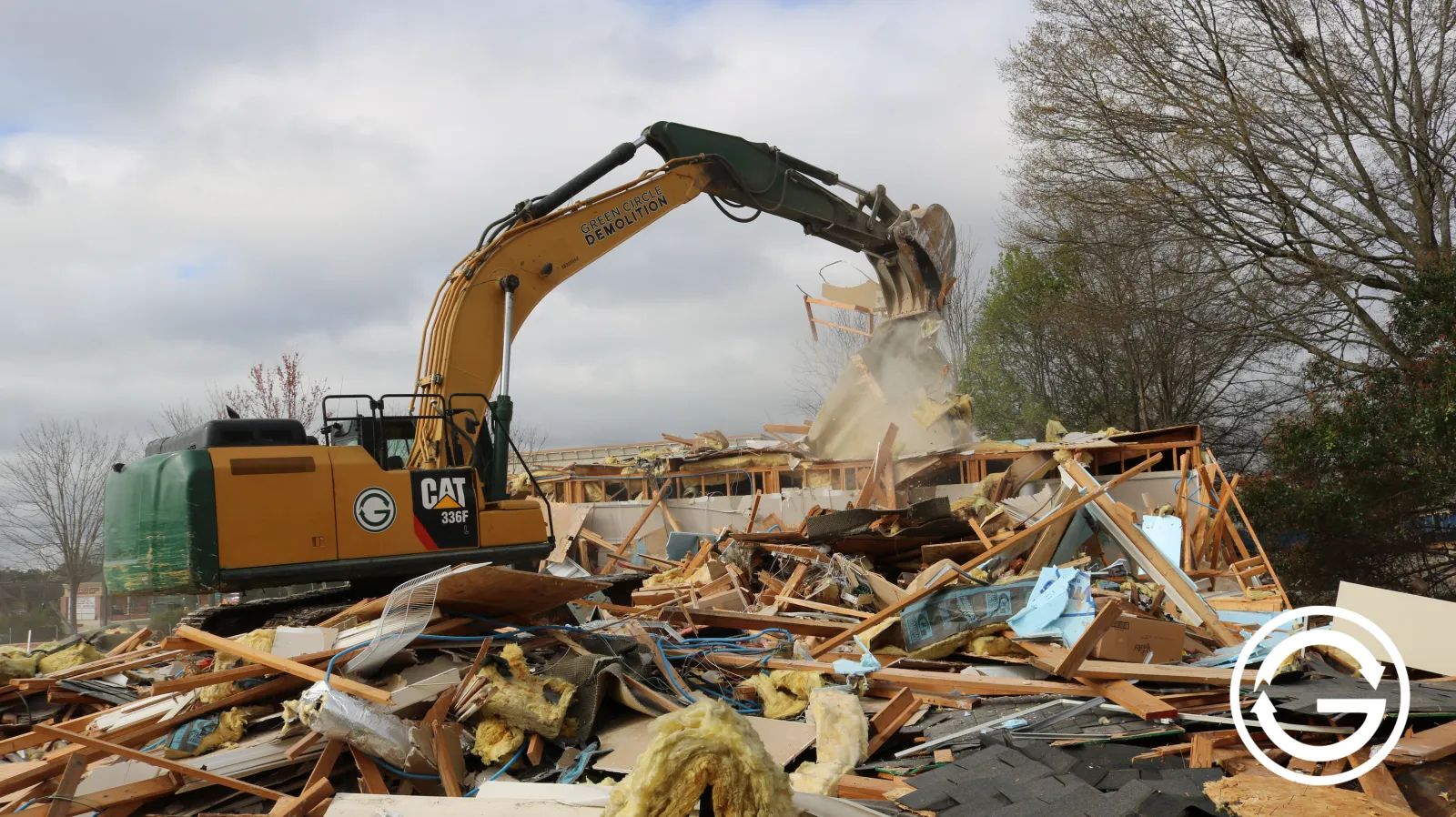
That said, it's always possible that a piece of equipment has to go down for maintenance on-site, even when well cared for. That downtime can cause all sorts of delays. For this very reason, we usually bring additional equipment on-site so that work can continue and down-time is minimized.
We Do a Thorough Initial Scoping
Here's an industry secret: A lot of demolition companies hate scoping out projects because it takes time to do correctly and general contractors or building owners don't want to pay to have it truly scoped. So what happens is, companies cut corners to get it done as quickly as possible and use the previous experience as estimations.
The problem there is that improper scoping can lead to change-orders, blown budgets, and timeline issues. This is especially the case with abatement or environmental considerations. Without a thorough assessment up-front, an abatement company ends up stumbling upon major challenges as they go, creating re-scope and costly start-and-stop workflow.
That is why we advise conducting a thorough scope for each project. We don't like surprises, and identifying issues up-front lets us get the job done quickly without having to constantly stop work.
We Take Safety Seriously
The federal government has a whole list of safety standards for construction demolition. And yet dozens of fatalities happen at demolition sites every year. Many of these come from non-compliance. They also stem from a culture of "doing just the minimum."
Safety protocols are not just a matter of checking off a box for safety compliance on an OSHA checklist. Remember, safety compliance outlines the absolute minimum that a company must do, according to the government. Companies that take safety seriously do more than the minimum!
Here at Green Circle Demolition, we've created a set of "turnkey" safety protocols. These are common safety protocols that the entire crew must follow, every time they are on a project. By having these protocols in place and making sure our crews follow them, we prevent accidents on-site, and that means less potential downtime. We also train our crews on those protocols and the proper use of safety equipment frequently.
We Schedule Work With a Dedicated Crew...
The norm in our industry is to have crews that are split between projects, with people coming in and out of a project site based on scheduling. While that might sound more efficient, it means that new people have to be "brought up to speed" on the project constantly.
Over the years we've learned that, if you want to minimize this "re-learning" and get the most efficiency out of a crew, you have to have a dedicated crew working on a project from the beginning. This way, everyone is familiar with the job right from the beginning, and no one needs to be brought up to speed at the start of their workday. Crew time is spent doing the work and solving problems, not having meetings to get everyone on the same page.
...But We Still Maintain Project Visibility
While we don't believe in having unnecessary updates to bring new people up to speed, we absolutely believe in sharing our progress regularly and documenting what we do. When there are members on the crew responsible for documenting the project and sharing updates, it guarantees that there is always someone with their eye on the timeline, making sure things stay on track. Sometimes a little accountability is all that is needed to stop those easily preventable demolition delays.
We've also found that frequent and detailed updates help to head off issues, too. Even with the most thorough scoping, there can be problems that develop along the way. Or, sometimes a client will just have an issue that they need to voice. With frequent updates, there are multiple stopping-points where we can have an open discussion about progress and barriers to it.
When that kind of visibility is not present at a project, it leads to "garden pathing"—work that is done incorrectly early on and not caught immediately, which in turn leads to backtracking the work and making costly adjustments.
The Takeaway: Don't Take Shortcuts
Just about every time we hear about a delay on a demolition project by another company, we come to find out it was because of a shortcut. These shortcuts—renting equipment cheaply, rushing the initial scoping, doing the absolute minimum for safety, shifting personnel between projects—might seem at first like they save time and effort. But they almost always cause problems further on down the line.
We have specifically crafted our turnkey protocols and procedures to minimize delays and downtime so that demolition projects get done on-time and within budget. More importantly, we believe in taking ownership of each and every project, to make sure it gets done right. If that kind of service sounds like what you need, contact us to find out more.